Lépjen offline állapotba az Player FM alkalmazással!
Eleven-I: Predicting Wind Blade Failures with Precision
Manage episode 445543323 series 2912702
This episode Allen and Joel speak with Bill Slatter, CEO of Eleven-I, about their innovative blade monitoring technology. Eleven-I’s sensors provide real-time data to detect and prevent blade damage, potentially reducing maintenance costs and improving turbine efficiency. Gain insights into the challenges of wind blade lifetimes, the importance of proactive monitoring, and the future of blade condition monitoring systems in the wind energy industry.
Sign up now for Uptime Tech News, our weekly email update on all things wind technology. This episode is sponsored by Weather Guard Lightning Tech. Learn more about Weather Guard’s StrikeTape Wind Turbine LPS retrofit. Follow the show on Facebook, YouTube, Twitter, Linkedin and visit Weather Guard on the web. And subscribe to Rosemary Barnes’ YouTube channel here. Have a question we can answer on the show? Email us!
Pardalote Consulting – https://www.pardaloteconsulting.com
Weather Guard Lightning Tech – www.weatherguardwind.com
Intelstor – https://www.intelstor.com
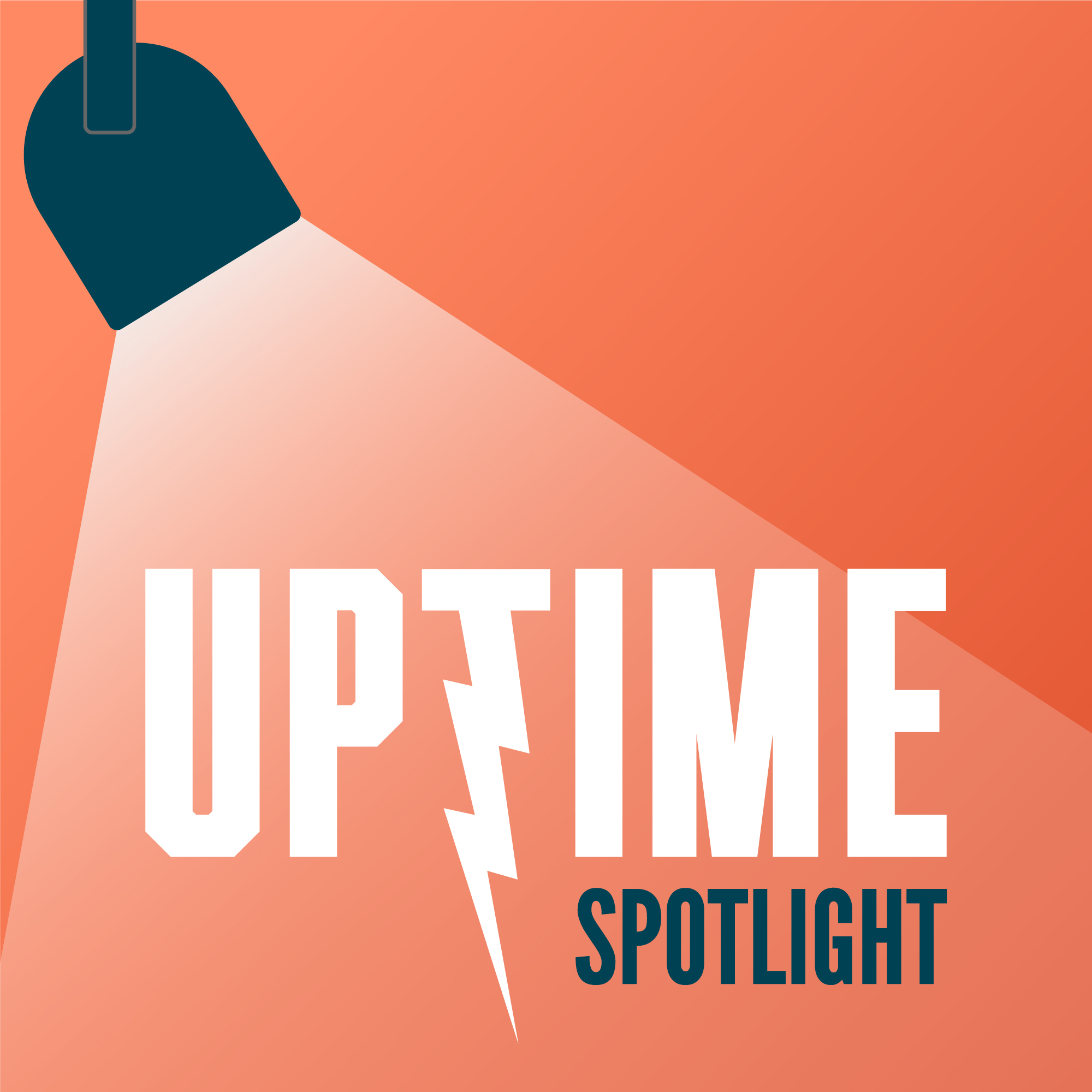
Allen Hall: Welcome to the Uptime Wind Energy Podcast. I’m your host, Allen Hall, joined by my co host, Joel Saxum. As we have all experienced, wind turbine blade failures can lead to costly downtime and repairs. And Eleven-I is tackling this challenge head on with their innovative monitoring technology. Their systems provide real time data that helps increase efficiency and reduce maintenance costs.
And if you are new to Eleven-I, they are based in the UK. Near Manchester, England. Today, we’re joined by Bill Slatter, CEO of Eleven-I. We’ll be discussing the challenges in Windblade Lifetimes, Eleven-I’s solutions, and the impact on the industry. Bill, welcome to the show.
Bill Slatter: Thanks for having me.
Allen Hall: There has been a number of horror stories over the last several months in regards to Blades And I know Eleven-I has been called into action on some of those because I’ve dealt with the operators on those projects but there does seem to be a lot of blade issues at the moment.
And it mostly, at least in my opinion it evolves from not knowing what is actually happening with the blade.
Bill Slatter: So one of the things that Eleven-I is trying to do is not just detect damage, but help understand what’s causing most of those damaging conditions. It’s something that we’ve. We’ve been trying to pioneer is yeah, picking out what causes damage, not just picking out when it’s happened.
Is that already too late? I think that’s one of the things that the industry is picking up on. We need to Obviously pick out that damage earlier on. What would happen if we could actually get to the point where we’re preempting damage and stopping it happening?
Joel Saxum: So I think Bill, that’s one of the things of course we’ve known each other for a couple of years now, and that was one of the things that originally, when I was in my blade life attracted me to you and your solution.
Of course, I like working with you because you’re a nice guy. But, on the other side of that, it is what Eleven-I brings to the table as far as its CMS technology, and you immediately caught me when we had our first call and you showed me a presentation about, and you’re like, this is an active movement of what’s happening in the blade now, And you guys are doing things rather than, hey, we’ve detected a crack, it’s, we have these physics engines, we’re trying to do, we can, we’re looking at modeling fatigue over lifetime, we’re trying to understand why these issues are happening, or being able to warn operators or give them flags of hey, you’re overloaded here, or you’ve got this going on, Before, and what we feel like a lot of other CMS systems do, they’re like, Hey, problem, flag, come and inspect.
So can you walk us through a little bit about what sets the Eleven-I solution apart from the rest of that Blade CMS marketplace?
Bill Slatter: Absolutely. I think one of the sort of things that perhaps differentiates us from some of our competitors is that we’re active in a number of similar markets.
So we’ve got systems that are being used for in blade test facilities to help understand the bit that blade behavior when they’re in the testing phase. We’ve also been used by OEMs to help understand the behavior of wind turbine blades. They’re the newest, it’s a prototype turbine. And they want to know how that may differ from models and actually see how that blade behaves in the real world.
So the type of work that we do in these engineering projects really help. help us to understand what real life looks like and what blade behavior should be, or maybe it shouldn’t be. And that helps us then get to the point where we can help people understand what is causing that damage. And also, I’ve said that before, but We have detected damage when it’s occurred, we’ve also been dropped onto blades that they know have damage or very high susceptibilities to damage and successfully detected those damage modes.
I think that’s the big thing is that, if we set our mission statement, it would be detect damage, detect the causes of damage, and then try and prevent damage.
Allen Hall: Yeah, it does seem particularly with newer blades, We don’t have a lot of service history. We don’t really know what those failure modes are.
And because as we’ve seen on a number of operators, the blade sets are made in different factories in different parts of the world that, which may have different materials built inside them and different approaches to building those blades. The mechanical response of. A set of blades on a particular turbine may not be the same response as the turbine next to it.
That is a huge problem area at the moment for the wind industry. What do we do about that? How, what is, what, first of all, what do you think is driving some of that besides manufacturing? Is it just because we don’t understand some of the physics involved? Are we guessing we’re getting newer, Modes of failure because of the blade length?
Bill Slatter: New technologies enormous blades, reductions of safety factors and then as shorter innovation time as possible this is why we’re in the position where we are. Nobody wants this to happen. But part of the way out of it is to use systems like ours to help understand what’s actually happening on your blades.
The blades are generally fairly neglected in terms of condition monitoring. Some of the bigger blades may have some sort of load sensing systems in there. But it’s not something that has been done as commonplace yet. But obviously the industry knows that requirement is coming.
We want to be part of it.
Joel Saxum: I had a customer that had a problem they knew was a highly susceptible to an issue. And when we scoured the market for what can we use to, to detect this, that what is that next level of CMS that can really dive down into frequencies and all these different kinds of things and have the engineering prowess behind it in the 11i team to be able to tell us what’s actually going on here.
We used you guys, and that installation was basically on that project. Now, of course, I’m sure they’re all different, but on that project it was three sensors in each blade. All amalgamated to one control box with power and comms to it. And then you guys were able to, of course, through your dashboard and everything, be able to see what was going on, map, look at trend lines over time, put some great reports together and help that client.
That was a specific case, right? We knew what we were looking for and we needed a piece of kit to do it. And I think what makes it something that shines to me here is that Alan and I have regular conversations with say like R and D test systems testing big blades and doing fantastic things in that realm.
But there is, there’s just some reality to, Putting sensors in advanced sensors and understanding what’s happening out in the real world, because you can only test so much, even if it’s hybrid testing, throw in some AI, some machine learning, the biggest freaking 25 megawatt generator test beds and all these things.
You can only test so much in a lab, but you really need to be able to dive in to get real data in the field. That’s something I think that sets you guys apart, the ability to collect that high frequency, real good data to be able to do the engineering projects from. And what I want to ask you is, and of course, in respect to any NDAs that you have in place, is there anything that you can share with us of a brief case study of something you guys have done or a problem you’ve solved for someone in the field.
Bill Slatter: There’s a number, obviously a number of case studies. The project that we worked together is helping the customer understand the best behavior that they wanted to eliminate. Through that project, we also picked up on some of the anomalous behavior that we detected. So whenever we get involved in any of these projects, we try and.
We, there’s often a problem statement from the customer, but we always will deploy all of our analytical methods to that data and highlight that to the customer. So I won’t go too deep into what was found there. But, we didn’t just go we went outside the scope of what we set out to do.
It’s probably worth talking a little bit about some of the work that we were done with OEMs. Because using the same equipment that we use for that we use in the field for problem solving when people know we have an issue like the type of project that you and I did together, Joel we use the same kit, and we may have a greater number of sensors, and we may be able to get further out down the blade, but we, this is essentially the same kit that’s used For these really in depth validation projects that’s used for these smaller projects.
And obviously every time you do a project there’s learnings from that. So the more systems you get out there, the more we’re able to offer all of our customers. And I hope that sort of that, that makes sense to you guys.
Allen Hall: It does. And as we have worked with a lot of operators that are buying 10 turbines, a hundred turbines, several hundred turbines.
I’m always shocked that they don’t know much about the blade performance before they start operating those turbines. And they don’t implement some sort of more integrated monitoring system onto the blades to actually see how the blades are performing in their particular site. And this is where I want to get into the little magic that Eleven Eye has in terms of what you’re actually doing to the blades and what you’re monitoring on the blades.
It is a relatively simple device from the outside, but you are putting some pretty smart brains into the blade.
Bill Slatter: Absolutely. What we set out to do is something that’s easily field deployable. I think I probably took, when we talked previously, I told you where my background was.
How I got into wind was through transport monitoring of nearly built. wind turbine blades. And I tried to use off the shelf kit, but they just, none of it did the job that we wanted to do. That led me into the development of our system. We can deploy our system in around half a day.
So that’ll be between two and three, three or three sensors per blade. And then some work in the hub and everything’s on the rotating side. And it’s something that’s, there’s a fairly practical job. We want some, we want a system that doesn’t need super precision or super specifically trained installers.
We want something that can be there’s field deployable and that’s what we’ve got. Yeah, it’s it’s Magnetic solvents are a solution and as I said before, we can play with a number of sensors per blade depending on what we want to look for.
Allen Hall: And the cost to install the sensors in the sensors themselves, what are we talking about in terms of cost per blade roughly?
Bill Slatter: Currently a system for a full turbine based on two sensors per blade is in the region of six to 7, 000 possibly a little bit less. We’ve got a new iteration that’s coming out very soon, which will hopefully reduce the cost. And yeah, so it’s not a, it’s not a particularly high cost system. And as I say, it’s something that we want to drive the cost down.
And yeah it’s something that it’s practical enough that people can potentially use their own techs to fit.
Allen Hall: That’s inexpensive if you’ve have new blades compared to the consequences that some of these operators are dealing with at the moment, because they just, don’t know the failure modes and what’s actually happening with the blade.
So with those couple of sensors installed in each of the blades, what are you then able to learn from the blade as it starts to rotate?
Bill Slatter: So as soon as it starts to rotate there’s initially a small phase of understanding what normal looks like. This, although that’s probably in the region of a couple of weeks, we start to learn, familiar with the output from that, that serves turbine.
If we’ve already seen that turbine before we know we’re expecting On top of that, we’ve got specific things that we’ll look out for that we would know about, we’ve got, we essentially what we do is when we’re on these projects you aim to categorize or characterize fault modes. So if you set off with a completely new turbine, that you set fairly wide boundaries for that type of failure mode, but it gives you an idea, it’s a bit like if cars were a mechanic working on a car they’ll have an idea of what that may mean if they see a specific, um, phenomena occurring.
So out the back of the system, we can give you ideas of how that blade is moving, the dynamics of it. We can tell you that effectively it’s a work done calculation. So that’s a really good way for us to understand whether there’s just abnormal behavior or whether the blades have been extremely excited by either weather.
And we have seen it where blades have been affected by pitch misalignment or also controller issues. And that, these are some of these things you can fix, we figured out and it’s something that was, yeah. And, but I think one of the things that. One of the things that we want to do is help people understand what, things that some things will get ignored because they’re not necessarily affecting how much energy the turbines producing, but it could be damaging that blade, there’s very secret things that people don’t, you don’t really necessarily understand or have vision on because it’s a, it could be something minor that you overlook within the SCADA data.
The reality is that there’s a fairly significant knock on to how much energy that those blades are experiencing. So we’ve also detected a number of of blade cracking faults and also root connection issues. So the root bolt connection is something that we’ve seen a couple of times where basically we’re using our sensors.
We can pick out either the delamination or just loose connections.
Allen Hall: All right. So for 6, 000. Dollars roughly you have an instrumented turbine if you’re spending, especially now, Joel, when you’re buying, it’s essentially no one’s buying less than a two megawatt generator. So it’s about two and a half million to somewhere in the in the seven megawatt generators, we’re starting to see on shore at the minute you’re paying upwards of nine, ten million dollars for those generators.
Six thousand dollars seems like it’s simple money to ensure that your turbine is operating properly and the blades are operating the way you think that they are. That makes complete sense to me. There’s a competitive
Joel Saxum: landscape, right? There’s a quite a few different systems out there. So what do you see for the future of this is a pretty broad question, but what do you see for the future of blade CMS?
Is it going to be something that everybody’s going to start to implement? Are you still going to see onesie twosies here and there for special cases, or what is your thoughts on that?
Bill Slatter: I’d imagine that people will. Prioritize high value problems. So we may see people do more trials on problematic platforms.
Every, all of the REMs have got issues. So there’s plenty to go out. But the ambition, and I think we will get there is that, there’s a a more joined up approach to O& M, at the moment it’s fairly spread out and people aren’t sharing information, I know it sounds a little bit fanciful, but if we got to that position where There is a sort of more joined up approach to RNM, then we could actually probably reduce the costs and have more uptime, and in the future have more reliable turbines.
That’s what we all want, right? For us, it’s a double edged sword, we see these big blade issues and we’re in the right place for it, but the reality is it’s not good for the wind industry.
Allen Hall: And we’ve run into a lot of blade teams at operators that really struggle to get data.
I’m always shocked by this, that. The first thing they want to know in any sort of blade defect situation that they’re trying to evaluate, they’re just, they’re handcuffed all the time because they just don’t have any information. And then, is it a serial defect? Where else should I be looking for this?
They just don’t have the tools. And then it makes sense for, especially Eleven Eye, to come in and provide the tools necessary to complete this task. And I know you’ve been working with a number of operators. What does that interface look like with the blade engineers when they come to you and say, Hey, I think we’re thinking we’re having problems.
Please help what happens next?
Bill Slatter: So usually we’d obviously have a meeting to discuss how we get the system installed And if we’re working with people with bladestemers Then very often we’ll meet directly once a week depending on the severity of issue. Maybe once every other week It all depends on the issue really and but we also work with other ISPs.
So in the past, we’ve worked with some of the companies that you’ve had on here before it’s a fairly small world and that, that offers. Basically, working with them offers a full solution to the customer of, not just what’s wrong, but what do you do about it, and how to do it.
And that, that, that’s a very key thing for us. So that’s something we’re very interested in doing is working with people that not only do we just say, hey, this is the problem, but then there’s that next step of fixing it. And. That that, and that’s what we want to happen. And the customer wants it to happen.
Allen Hall: How quickly can you get some turbines instrumented and get that dashboard going and start getting those blade engineers some real hard, hard data?
Bill Slatter: If we’ve got the systems on the shelf, then we’ll end up with, if it’s in the US, then generally we’ll have the systems out there within two to three weeks.
And as I say, depending on the the requirement and the fitting crew we’d hope to have. I think I’d say the use of the first system will usually take a day and then the subsequent systems will take around half a day. As soon as those systems have turned on, then we’ll start getting useful data.
And as I say, we’ve got a sufficient analytical tool library that we can start being useful from day one. And then the sort of the real depth and a learning school from when you’ve had a period of learning from that turbine. The ambition for us is, that we’re.
We’re fitted for long term projects and we can help people understand the type of the behavior of their blades and the life that potentially use that information for lifetime extension or for O& M scheduling. We can help you, you can tell you straight away which turbines are having are seeing more high energy events.
And it’s really interesting seeing this on, on, on wind farms, you can have turbines that are only a few hundred meters apart and they’re seeing radically different levels of energy on those blades, and when I say energy, basically they’re much higher movements from on, on one turbine.
Joel Saxum: Bill, let me ask you a question then. Have you been approached by any of these? Because we did patent reviews and some other things we were talking about the other day and there’s the Windescos and the, all these wake steering ideas. Have you been approached by someone to validate one of these wake steering ideas offshore?
Bill Slatter: We may have been, we may have talked to somebody about that because obviously, that, then it starts getting really interesting, right? Because it’s that big picture stuff. And that was very exciting.
Allen Hall: How would you do that without having some, at least some decent load measurements and how the blades are reacting to the inputs you’re adding to the farm.
You have to have some data to show that you wouldn’t destroy the blades over time, right?
Bill Slatter: Yep. And obviously we can help with that. So we can give you those, we can give you those comparative loads for the bla individual blades. And yeah, that’s pretty straightforward. If we want, we can also calibrate to give a absolute strain measurement.
A load measurement, sorry as well, which is something we’ve done in the past.
Joel Saxum: Yeah. If I was someone deploying a new, any new platform specifically in a new geography as well and in difficult places, remote places, offshore, even like Allen in my mind, the one that comes to, of course, sun Zia.
Because Sunzea’s two brand new turbine models out in the middle of nowhere in New Mexico. It would be nice to have some of those turbines instrumented because it’s a new geography, it’s a new turbine type. And just to understand what’s actually happening in those blades as they experience their first, first few seasons, at least In production because that’s like we said earlier in the recording here, we’ve been ramping up rotor sizes so fast and we’re so far ahead of this curve and we’re trying to, save weight and we’re affecting And those are the kind of things as these blades grow.
So I think it’s smart for people to start doing this from the development side. So where are your customers right now, Bill where on the world?
Bill Slatter: The majority of our customers are in the U S we’ve got some in Europe as well, but the U S just seems a little bit braver in adoption of new technologies.
I think the European market is it’s a bit more mature and they do things the way they do it. But that’s changing, anecdotally, we’ve had customers that we spoke to years ago right at the inception of 11i and they’ve been having problems and, the first time you see a problem, you might go that was a one off.
The second time, or the third time, maybe you want to know a bit more about it.
Allen Hall: And if a future customer wants to connect with you, how do they find you on the web?
Bill Slatter: So there’s the Eleven-I website, which is eleven-i.com. There’s plenty of links to get in touch with us there. Or you can look me up on LinkedIn or the company on LinkedIn and I encourage answering you that way.
Allen Hall: So Bill, it’s been great having you on the podcast. I’ve seen your work all around the United States. A lot of companies are using 11i to get the data that they need to make smart decisions. Your sensors are leading that. And if you need to reach out to 11i, go to the website, 11 i. com. Bill, thank you so much for being on the program.
Bill Slatter: Thank you very much, Allen and Joel. Really appreciate it. And hopefully we’ll meet again in person soon.
364 epizódok
Manage episode 445543323 series 2912702
This episode Allen and Joel speak with Bill Slatter, CEO of Eleven-I, about their innovative blade monitoring technology. Eleven-I’s sensors provide real-time data to detect and prevent blade damage, potentially reducing maintenance costs and improving turbine efficiency. Gain insights into the challenges of wind blade lifetimes, the importance of proactive monitoring, and the future of blade condition monitoring systems in the wind energy industry.
Sign up now for Uptime Tech News, our weekly email update on all things wind technology. This episode is sponsored by Weather Guard Lightning Tech. Learn more about Weather Guard’s StrikeTape Wind Turbine LPS retrofit. Follow the show on Facebook, YouTube, Twitter, Linkedin and visit Weather Guard on the web. And subscribe to Rosemary Barnes’ YouTube channel here. Have a question we can answer on the show? Email us!
Pardalote Consulting – https://www.pardaloteconsulting.com
Weather Guard Lightning Tech – www.weatherguardwind.com
Intelstor – https://www.intelstor.com
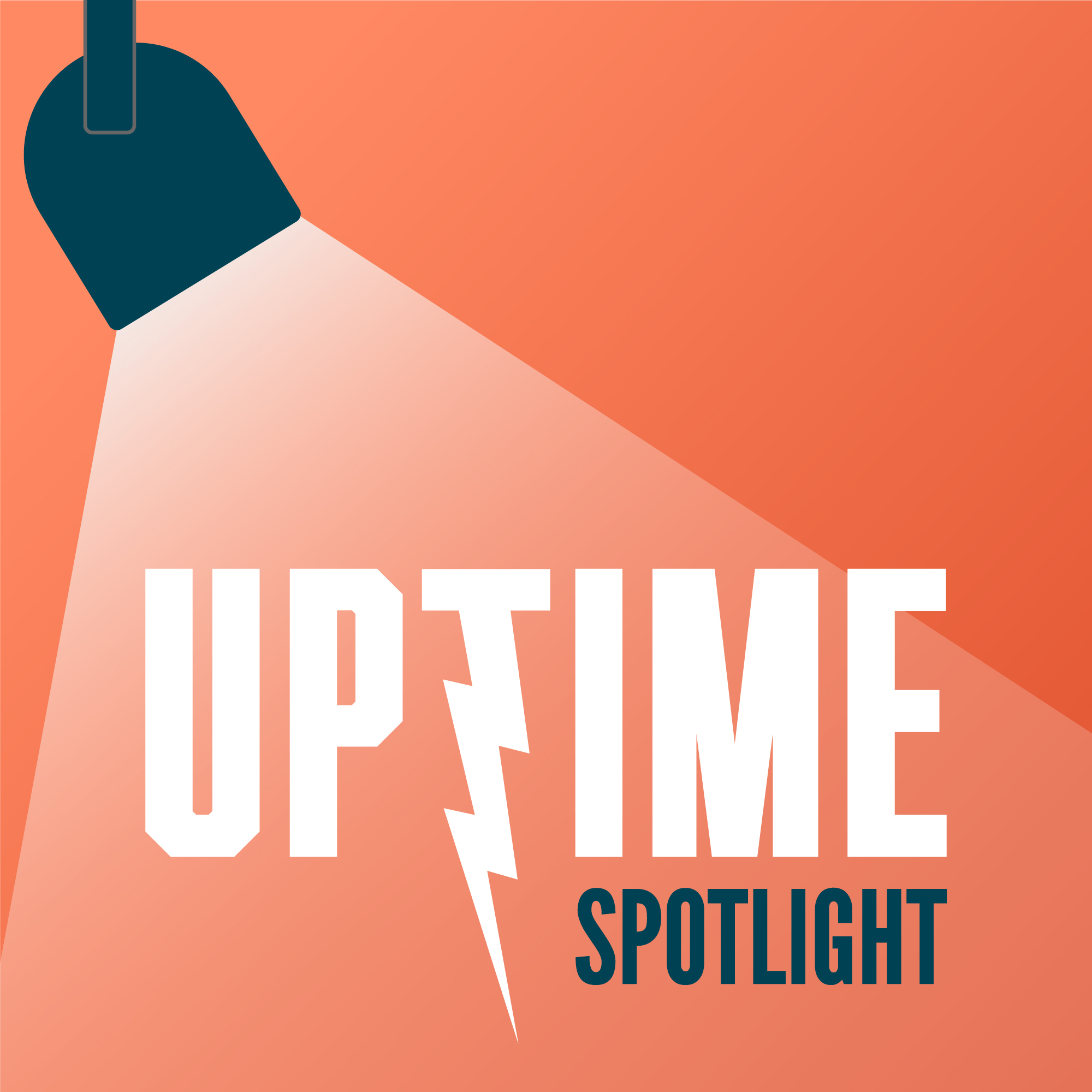
Allen Hall: Welcome to the Uptime Wind Energy Podcast. I’m your host, Allen Hall, joined by my co host, Joel Saxum. As we have all experienced, wind turbine blade failures can lead to costly downtime and repairs. And Eleven-I is tackling this challenge head on with their innovative monitoring technology. Their systems provide real time data that helps increase efficiency and reduce maintenance costs.
And if you are new to Eleven-I, they are based in the UK. Near Manchester, England. Today, we’re joined by Bill Slatter, CEO of Eleven-I. We’ll be discussing the challenges in Windblade Lifetimes, Eleven-I’s solutions, and the impact on the industry. Bill, welcome to the show.
Bill Slatter: Thanks for having me.
Allen Hall: There has been a number of horror stories over the last several months in regards to Blades And I know Eleven-I has been called into action on some of those because I’ve dealt with the operators on those projects but there does seem to be a lot of blade issues at the moment.
And it mostly, at least in my opinion it evolves from not knowing what is actually happening with the blade.
Bill Slatter: So one of the things that Eleven-I is trying to do is not just detect damage, but help understand what’s causing most of those damaging conditions. It’s something that we’ve. We’ve been trying to pioneer is yeah, picking out what causes damage, not just picking out when it’s happened.
Is that already too late? I think that’s one of the things that the industry is picking up on. We need to Obviously pick out that damage earlier on. What would happen if we could actually get to the point where we’re preempting damage and stopping it happening?
Joel Saxum: So I think Bill, that’s one of the things of course we’ve known each other for a couple of years now, and that was one of the things that originally, when I was in my blade life attracted me to you and your solution.
Of course, I like working with you because you’re a nice guy. But, on the other side of that, it is what Eleven-I brings to the table as far as its CMS technology, and you immediately caught me when we had our first call and you showed me a presentation about, and you’re like, this is an active movement of what’s happening in the blade now, And you guys are doing things rather than, hey, we’ve detected a crack, it’s, we have these physics engines, we’re trying to do, we can, we’re looking at modeling fatigue over lifetime, we’re trying to understand why these issues are happening, or being able to warn operators or give them flags of hey, you’re overloaded here, or you’ve got this going on, Before, and what we feel like a lot of other CMS systems do, they’re like, Hey, problem, flag, come and inspect.
So can you walk us through a little bit about what sets the Eleven-I solution apart from the rest of that Blade CMS marketplace?
Bill Slatter: Absolutely. I think one of the sort of things that perhaps differentiates us from some of our competitors is that we’re active in a number of similar markets.
So we’ve got systems that are being used for in blade test facilities to help understand the bit that blade behavior when they’re in the testing phase. We’ve also been used by OEMs to help understand the behavior of wind turbine blades. They’re the newest, it’s a prototype turbine. And they want to know how that may differ from models and actually see how that blade behaves in the real world.
So the type of work that we do in these engineering projects really help. help us to understand what real life looks like and what blade behavior should be, or maybe it shouldn’t be. And that helps us then get to the point where we can help people understand what is causing that damage. And also, I’ve said that before, but We have detected damage when it’s occurred, we’ve also been dropped onto blades that they know have damage or very high susceptibilities to damage and successfully detected those damage modes.
I think that’s the big thing is that, if we set our mission statement, it would be detect damage, detect the causes of damage, and then try and prevent damage.
Allen Hall: Yeah, it does seem particularly with newer blades, We don’t have a lot of service history. We don’t really know what those failure modes are.
And because as we’ve seen on a number of operators, the blade sets are made in different factories in different parts of the world that, which may have different materials built inside them and different approaches to building those blades. The mechanical response of. A set of blades on a particular turbine may not be the same response as the turbine next to it.
That is a huge problem area at the moment for the wind industry. What do we do about that? How, what is, what, first of all, what do you think is driving some of that besides manufacturing? Is it just because we don’t understand some of the physics involved? Are we guessing we’re getting newer, Modes of failure because of the blade length?
Bill Slatter: New technologies enormous blades, reductions of safety factors and then as shorter innovation time as possible this is why we’re in the position where we are. Nobody wants this to happen. But part of the way out of it is to use systems like ours to help understand what’s actually happening on your blades.
The blades are generally fairly neglected in terms of condition monitoring. Some of the bigger blades may have some sort of load sensing systems in there. But it’s not something that has been done as commonplace yet. But obviously the industry knows that requirement is coming.
We want to be part of it.
Joel Saxum: I had a customer that had a problem they knew was a highly susceptible to an issue. And when we scoured the market for what can we use to, to detect this, that what is that next level of CMS that can really dive down into frequencies and all these different kinds of things and have the engineering prowess behind it in the 11i team to be able to tell us what’s actually going on here.
We used you guys, and that installation was basically on that project. Now, of course, I’m sure they’re all different, but on that project it was three sensors in each blade. All amalgamated to one control box with power and comms to it. And then you guys were able to, of course, through your dashboard and everything, be able to see what was going on, map, look at trend lines over time, put some great reports together and help that client.
That was a specific case, right? We knew what we were looking for and we needed a piece of kit to do it. And I think what makes it something that shines to me here is that Alan and I have regular conversations with say like R and D test systems testing big blades and doing fantastic things in that realm.
But there is, there’s just some reality to, Putting sensors in advanced sensors and understanding what’s happening out in the real world, because you can only test so much, even if it’s hybrid testing, throw in some AI, some machine learning, the biggest freaking 25 megawatt generator test beds and all these things.
You can only test so much in a lab, but you really need to be able to dive in to get real data in the field. That’s something I think that sets you guys apart, the ability to collect that high frequency, real good data to be able to do the engineering projects from. And what I want to ask you is, and of course, in respect to any NDAs that you have in place, is there anything that you can share with us of a brief case study of something you guys have done or a problem you’ve solved for someone in the field.
Bill Slatter: There’s a number, obviously a number of case studies. The project that we worked together is helping the customer understand the best behavior that they wanted to eliminate. Through that project, we also picked up on some of the anomalous behavior that we detected. So whenever we get involved in any of these projects, we try and.
We, there’s often a problem statement from the customer, but we always will deploy all of our analytical methods to that data and highlight that to the customer. So I won’t go too deep into what was found there. But, we didn’t just go we went outside the scope of what we set out to do.
It’s probably worth talking a little bit about some of the work that we were done with OEMs. Because using the same equipment that we use for that we use in the field for problem solving when people know we have an issue like the type of project that you and I did together, Joel we use the same kit, and we may have a greater number of sensors, and we may be able to get further out down the blade, but we, this is essentially the same kit that’s used For these really in depth validation projects that’s used for these smaller projects.
And obviously every time you do a project there’s learnings from that. So the more systems you get out there, the more we’re able to offer all of our customers. And I hope that sort of that, that makes sense to you guys.
Allen Hall: It does. And as we have worked with a lot of operators that are buying 10 turbines, a hundred turbines, several hundred turbines.
I’m always shocked that they don’t know much about the blade performance before they start operating those turbines. And they don’t implement some sort of more integrated monitoring system onto the blades to actually see how the blades are performing in their particular site. And this is where I want to get into the little magic that Eleven Eye has in terms of what you’re actually doing to the blades and what you’re monitoring on the blades.
It is a relatively simple device from the outside, but you are putting some pretty smart brains into the blade.
Bill Slatter: Absolutely. What we set out to do is something that’s easily field deployable. I think I probably took, when we talked previously, I told you where my background was.
How I got into wind was through transport monitoring of nearly built. wind turbine blades. And I tried to use off the shelf kit, but they just, none of it did the job that we wanted to do. That led me into the development of our system. We can deploy our system in around half a day.
So that’ll be between two and three, three or three sensors per blade. And then some work in the hub and everything’s on the rotating side. And it’s something that’s, there’s a fairly practical job. We want some, we want a system that doesn’t need super precision or super specifically trained installers.
We want something that can be there’s field deployable and that’s what we’ve got. Yeah, it’s it’s Magnetic solvents are a solution and as I said before, we can play with a number of sensors per blade depending on what we want to look for.
Allen Hall: And the cost to install the sensors in the sensors themselves, what are we talking about in terms of cost per blade roughly?
Bill Slatter: Currently a system for a full turbine based on two sensors per blade is in the region of six to 7, 000 possibly a little bit less. We’ve got a new iteration that’s coming out very soon, which will hopefully reduce the cost. And yeah, so it’s not a, it’s not a particularly high cost system. And as I say, it’s something that we want to drive the cost down.
And yeah it’s something that it’s practical enough that people can potentially use their own techs to fit.
Allen Hall: That’s inexpensive if you’ve have new blades compared to the consequences that some of these operators are dealing with at the moment, because they just, don’t know the failure modes and what’s actually happening with the blade.
So with those couple of sensors installed in each of the blades, what are you then able to learn from the blade as it starts to rotate?
Bill Slatter: So as soon as it starts to rotate there’s initially a small phase of understanding what normal looks like. This, although that’s probably in the region of a couple of weeks, we start to learn, familiar with the output from that, that serves turbine.
If we’ve already seen that turbine before we know we’re expecting On top of that, we’ve got specific things that we’ll look out for that we would know about, we’ve got, we essentially what we do is when we’re on these projects you aim to categorize or characterize fault modes. So if you set off with a completely new turbine, that you set fairly wide boundaries for that type of failure mode, but it gives you an idea, it’s a bit like if cars were a mechanic working on a car they’ll have an idea of what that may mean if they see a specific, um, phenomena occurring.
So out the back of the system, we can give you ideas of how that blade is moving, the dynamics of it. We can tell you that effectively it’s a work done calculation. So that’s a really good way for us to understand whether there’s just abnormal behavior or whether the blades have been extremely excited by either weather.
And we have seen it where blades have been affected by pitch misalignment or also controller issues. And that, these are some of these things you can fix, we figured out and it’s something that was, yeah. And, but I think one of the things that. One of the things that we want to do is help people understand what, things that some things will get ignored because they’re not necessarily affecting how much energy the turbines producing, but it could be damaging that blade, there’s very secret things that people don’t, you don’t really necessarily understand or have vision on because it’s a, it could be something minor that you overlook within the SCADA data.
The reality is that there’s a fairly significant knock on to how much energy that those blades are experiencing. So we’ve also detected a number of of blade cracking faults and also root connection issues. So the root bolt connection is something that we’ve seen a couple of times where basically we’re using our sensors.
We can pick out either the delamination or just loose connections.
Allen Hall: All right. So for 6, 000. Dollars roughly you have an instrumented turbine if you’re spending, especially now, Joel, when you’re buying, it’s essentially no one’s buying less than a two megawatt generator. So it’s about two and a half million to somewhere in the in the seven megawatt generators, we’re starting to see on shore at the minute you’re paying upwards of nine, ten million dollars for those generators.
Six thousand dollars seems like it’s simple money to ensure that your turbine is operating properly and the blades are operating the way you think that they are. That makes complete sense to me. There’s a competitive
Joel Saxum: landscape, right? There’s a quite a few different systems out there. So what do you see for the future of this is a pretty broad question, but what do you see for the future of blade CMS?
Is it going to be something that everybody’s going to start to implement? Are you still going to see onesie twosies here and there for special cases, or what is your thoughts on that?
Bill Slatter: I’d imagine that people will. Prioritize high value problems. So we may see people do more trials on problematic platforms.
Every, all of the REMs have got issues. So there’s plenty to go out. But the ambition, and I think we will get there is that, there’s a a more joined up approach to O& M, at the moment it’s fairly spread out and people aren’t sharing information, I know it sounds a little bit fanciful, but if we got to that position where There is a sort of more joined up approach to RNM, then we could actually probably reduce the costs and have more uptime, and in the future have more reliable turbines.
That’s what we all want, right? For us, it’s a double edged sword, we see these big blade issues and we’re in the right place for it, but the reality is it’s not good for the wind industry.
Allen Hall: And we’ve run into a lot of blade teams at operators that really struggle to get data.
I’m always shocked by this, that. The first thing they want to know in any sort of blade defect situation that they’re trying to evaluate, they’re just, they’re handcuffed all the time because they just don’t have any information. And then, is it a serial defect? Where else should I be looking for this?
They just don’t have the tools. And then it makes sense for, especially Eleven Eye, to come in and provide the tools necessary to complete this task. And I know you’ve been working with a number of operators. What does that interface look like with the blade engineers when they come to you and say, Hey, I think we’re thinking we’re having problems.
Please help what happens next?
Bill Slatter: So usually we’d obviously have a meeting to discuss how we get the system installed And if we’re working with people with bladestemers Then very often we’ll meet directly once a week depending on the severity of issue. Maybe once every other week It all depends on the issue really and but we also work with other ISPs.
So in the past, we’ve worked with some of the companies that you’ve had on here before it’s a fairly small world and that, that offers. Basically, working with them offers a full solution to the customer of, not just what’s wrong, but what do you do about it, and how to do it.
And that, that, that’s a very key thing for us. So that’s something we’re very interested in doing is working with people that not only do we just say, hey, this is the problem, but then there’s that next step of fixing it. And. That that, and that’s what we want to happen. And the customer wants it to happen.
Allen Hall: How quickly can you get some turbines instrumented and get that dashboard going and start getting those blade engineers some real hard, hard data?
Bill Slatter: If we’ve got the systems on the shelf, then we’ll end up with, if it’s in the US, then generally we’ll have the systems out there within two to three weeks.
And as I say, depending on the the requirement and the fitting crew we’d hope to have. I think I’d say the use of the first system will usually take a day and then the subsequent systems will take around half a day. As soon as those systems have turned on, then we’ll start getting useful data.
And as I say, we’ve got a sufficient analytical tool library that we can start being useful from day one. And then the sort of the real depth and a learning school from when you’ve had a period of learning from that turbine. The ambition for us is, that we’re.
We’re fitted for long term projects and we can help people understand the type of the behavior of their blades and the life that potentially use that information for lifetime extension or for O& M scheduling. We can help you, you can tell you straight away which turbines are having are seeing more high energy events.
And it’s really interesting seeing this on, on, on wind farms, you can have turbines that are only a few hundred meters apart and they’re seeing radically different levels of energy on those blades, and when I say energy, basically they’re much higher movements from on, on one turbine.
Joel Saxum: Bill, let me ask you a question then. Have you been approached by any of these? Because we did patent reviews and some other things we were talking about the other day and there’s the Windescos and the, all these wake steering ideas. Have you been approached by someone to validate one of these wake steering ideas offshore?
Bill Slatter: We may have been, we may have talked to somebody about that because obviously, that, then it starts getting really interesting, right? Because it’s that big picture stuff. And that was very exciting.
Allen Hall: How would you do that without having some, at least some decent load measurements and how the blades are reacting to the inputs you’re adding to the farm.
You have to have some data to show that you wouldn’t destroy the blades over time, right?
Bill Slatter: Yep. And obviously we can help with that. So we can give you those, we can give you those comparative loads for the bla individual blades. And yeah, that’s pretty straightforward. If we want, we can also calibrate to give a absolute strain measurement.
A load measurement, sorry as well, which is something we’ve done in the past.
Joel Saxum: Yeah. If I was someone deploying a new, any new platform specifically in a new geography as well and in difficult places, remote places, offshore, even like Allen in my mind, the one that comes to, of course, sun Zia.
Because Sunzea’s two brand new turbine models out in the middle of nowhere in New Mexico. It would be nice to have some of those turbines instrumented because it’s a new geography, it’s a new turbine type. And just to understand what’s actually happening in those blades as they experience their first, first few seasons, at least In production because that’s like we said earlier in the recording here, we’ve been ramping up rotor sizes so fast and we’re so far ahead of this curve and we’re trying to, save weight and we’re affecting And those are the kind of things as these blades grow.
So I think it’s smart for people to start doing this from the development side. So where are your customers right now, Bill where on the world?
Bill Slatter: The majority of our customers are in the U S we’ve got some in Europe as well, but the U S just seems a little bit braver in adoption of new technologies.
I think the European market is it’s a bit more mature and they do things the way they do it. But that’s changing, anecdotally, we’ve had customers that we spoke to years ago right at the inception of 11i and they’ve been having problems and, the first time you see a problem, you might go that was a one off.
The second time, or the third time, maybe you want to know a bit more about it.
Allen Hall: And if a future customer wants to connect with you, how do they find you on the web?
Bill Slatter: So there’s the Eleven-I website, which is eleven-i.com. There’s plenty of links to get in touch with us there. Or you can look me up on LinkedIn or the company on LinkedIn and I encourage answering you that way.
Allen Hall: So Bill, it’s been great having you on the podcast. I’ve seen your work all around the United States. A lot of companies are using 11i to get the data that they need to make smart decisions. Your sensors are leading that. And if you need to reach out to 11i, go to the website, 11 i. com. Bill, thank you so much for being on the program.
Bill Slatter: Thank you very much, Allen and Joel. Really appreciate it. And hopefully we’ll meet again in person soon.
364 epizódok
Minden epizód
×Üdvözlünk a Player FM-nél!
A Player FM lejátszó az internetet böngészi a kiváló minőségű podcastok után, hogy ön élvezhesse azokat. Ez a legjobb podcast-alkalmazás, Androidon, iPhone-on és a weben is működik. Jelentkezzen be az feliratkozások szinkronizálásához az eszközök között.